Advanced materials / Lightweight materials /
Metal foam in space application
The main advantage of the use of aluminium or magnesium foam in space applications is the possibility to manufacture complex and potentially large metallic parts directly in space, without need to launch voluminous structures from the Earth.
Due to expanded porous shape (inside porosity of min. 85%) it is expected that foamed components made of lightweight metals will possess very high stiffness to weight ratio that is comparable with current composites or better. Most of the properties can be adjusted by porosity level, what enables tailoring properties of future components without need to change installed technology and molds. The use of metal foam for space structures instead of plastics or ceramics would also be beneficial because the foams:
- retain satisfactory mechanical properties and plasticity at low temperatures
- can survive mechanical impacts have due to sufficient plasticity and compressibility (it is frequently used as crash energy absorbing material)
- conduct electricity and the structure thus can be utilized as efficient conductor instead of cables
- damp (attenuate) noise and vibrations
- are stable in electromagnetic field, do not suffer from UV radiation, etc.
- do not suffer from thermal distorsons due to excellent heat conduction, high stiffness and adjustable yield stress
- (by porosity) thermal stresses in the structure are significantly reduced.
Inside porosity of the foam reduces apparent density of final component below 1kg/liter and creates large cross sections with high cross-sectional moments of inertia in all directions what is beneficial for significant weight reduction in stiffness driven design. The components are made by foaming in suitable molds which gives them surface skin having complexity, precision and appearance similar as in case of traditional casting.
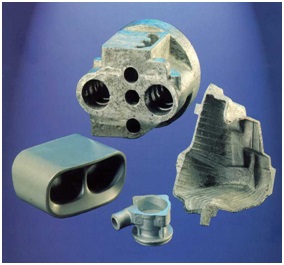
Foamed components
There are crucial differences in comparison to standard casting techniques:
- For given weight of the components the foamed volume is 5-10 times larger than the volume of standard casting
- The mould cavity is filled by thermal expansion (foaming) of suitable foamable feedstock placed in the mould – the driving force is development of gases inside softened (melted) feedstock that create pores inside feedstock and expands its volume until full cavity is filled with the foam. The feedstock expands on heating (melting); the expansion continues until all feedstock is entirely melted. The expansion rate depends on amount of foaming agent admixed into feedstock – i.e. the driving force enabling mould filling is implemented in the feedstock and there is no need on “external power”. Such “foaming process” is not limited by wall thickness of final component, nor by its complexity or size. In traditional casting technology the mould cavity is filled by molten metal what brings a lot of constraints on final part, associated with wall thickness-, complexity- and size limits and also with solidification shrinkage. Moreover the mold filling during casting requires some kind of driving force (gravity or pressure), that is not easily available in space.
- There are very low requirements on foaming mold; the mold can be made of thin steel sheet, machined graphite, sand etc. It is expected that the mold for manufacturing of components (modules) will be brought from the Earth and then used repeatedly for manufacturing of >1000 pcs in the same mold (this was approved in previous projects). In the future it is envisaged to print (3D) the molds directly in space even from lunar regolith (not included in this work).
- The novel patented technique enables foaming in the “cold” molds (e.g. printed regolith molds), whereas the melting of foamable feedstock is conducted using superheated melt poured into mold cavity. This technique enables manufacturing of hybrid casting having part made of foam and part made of bulk metal.
- When strong reinforcing wires are inserted into mold cavity, they are embedded and fixed in the foam during foaming thus making reinforced foam (similar approach as in the case of steel reinforced concrete). In such case ultralight foam with large cross section contributes to stiffness, and strong wire brings high tensile or bending strength. The embedded wires can be used for fixing of foamed modules together, eventually for stiffening the whole lightweight truss structure made of foamed struts components (via stretching of joined wires).
- There are also several advantages for foaming in space:
- existing vacuum and absence of oxygen enhance foam expansion (there is no oxidation of expansion front and lower amount of foaming agent is required)
- no problems with entrapped air when foaming in vacuum (the mold can be hermetically tight – this option leads to pressurizing the foam until full solidification and is thus beneficial for surface quality of the foam and complexity of the component shape)
- there is no danger of melt drainage in foam cell walls because of very low gravity
Foaming in space requires:
- Suitable metallic foamable feedstock granulate (from the Earth – the volume of granulate is about 10 times lower than the volume of final component to be foamed)
- Suitable mold for foaming (delivered from the Earth or made by 3D printing in the future, lunar regolith with appropriate binder can also be suitable material for making molds – similarly as sand molds)
- Energy for foaming –energy for melting feedstock and preheating the mold is needed. Approximately 1,5 MJ (net heat) is needed to foam 1 kg of Al- or Mg- alloy. Such energy can be easily provided by collector of solar heat. 1m2 of solar collector may provide heat ~ 3MJ per hour; the mold for profile foaming can be placed in focus of parabolic collector. It is expected to foam profiles having weight of ~0.1kg/m, i.e. supply of energy ~ 200 kJ/m is required. Expected length of the profile is ~ 10 m, i.e 2MJ heat is totally required. The parabolic radiator channel (width of 1 m, length 10 m has potential net power 13 kW, i.e. 46.8 MJ per hour) so there is a good chance to foam 50 m of profiles per hour.
- The radiator for foaming of profiles needs to be delivered from the Earth (the weight will be capitalized in continuous production of profiles for long time)
- Robotic equipment for necessary manipulation and assembly - needs to be delivered from the Earth (the weight will be capitalized in continuous production of foamed modules for long time)
The foaming itself is a simple and relatively quick manufacturing method with a production rate for one part in couple of minutes, what makes strong benefits especially if compared to 3D printing. The mold itself gives the foamed part shape and accuracy, so alternative components can be manufactured easily by changing the mold. As almost all properties of the foamed part strongly depend on porosity, they can be tailored even without need to change the mold. The porosity can be adjusted by proper amount of foaming agent admixed into foamable feedstock. Since the feedstock is delivered from the Earth this “property-tailoring-approach will not require any cost intensive treatment in space.
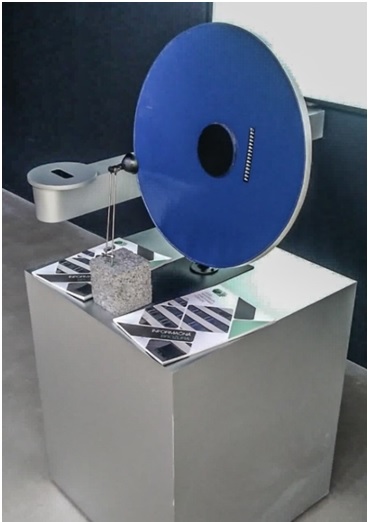
Parable of aluminium foam
A model of a heat shield made of aluminium foam in the shape of a parabolic dish with a diameter of 60 cm. The unique construction allows to maintain a constant temperature difference between the inner and outer side of the dish in a suitable orbit, which can be used to continuously generate mechanical energy resp. electricity even in the absence of several hours of sunlight. The weight of the dish is 1200 g, the volume is 7 dm
3. The volume of foamable feedstock granulate that needs to be launched from the Earth to foam the dish necessary to foam the dish is just 0,5 dm
3.